Novartis Pharmaceuticals, one of the top four global research and development centers of Novartis in Switzerland, consists of a pilot plant, three chemical active pharmaceutical ingredient (API) production plants, as well as tank farms, recovery units, and utility systems.
Novartis Pharmaceuticals Suzhou BATCH Project
The project aims to upgrade the existing semi-automatic production mode to a fully automated batch production mode at Novartis Pharmaceuticals Suzhou. It will also undergo Good Manufacturing Practice (GMP) validation according to FDA standards. The main technical challenges lie in the process digestion and program coding of control modules (EM) for temperature control, pressure control, material transfer, etc., in the reaction vessel. A formulation (Recipe) will be created to enable one-click start and achieve fully automated production. Furthermore, it will generate reports and data that comply with the data integrity requirements defined by CFR21 PAR11.
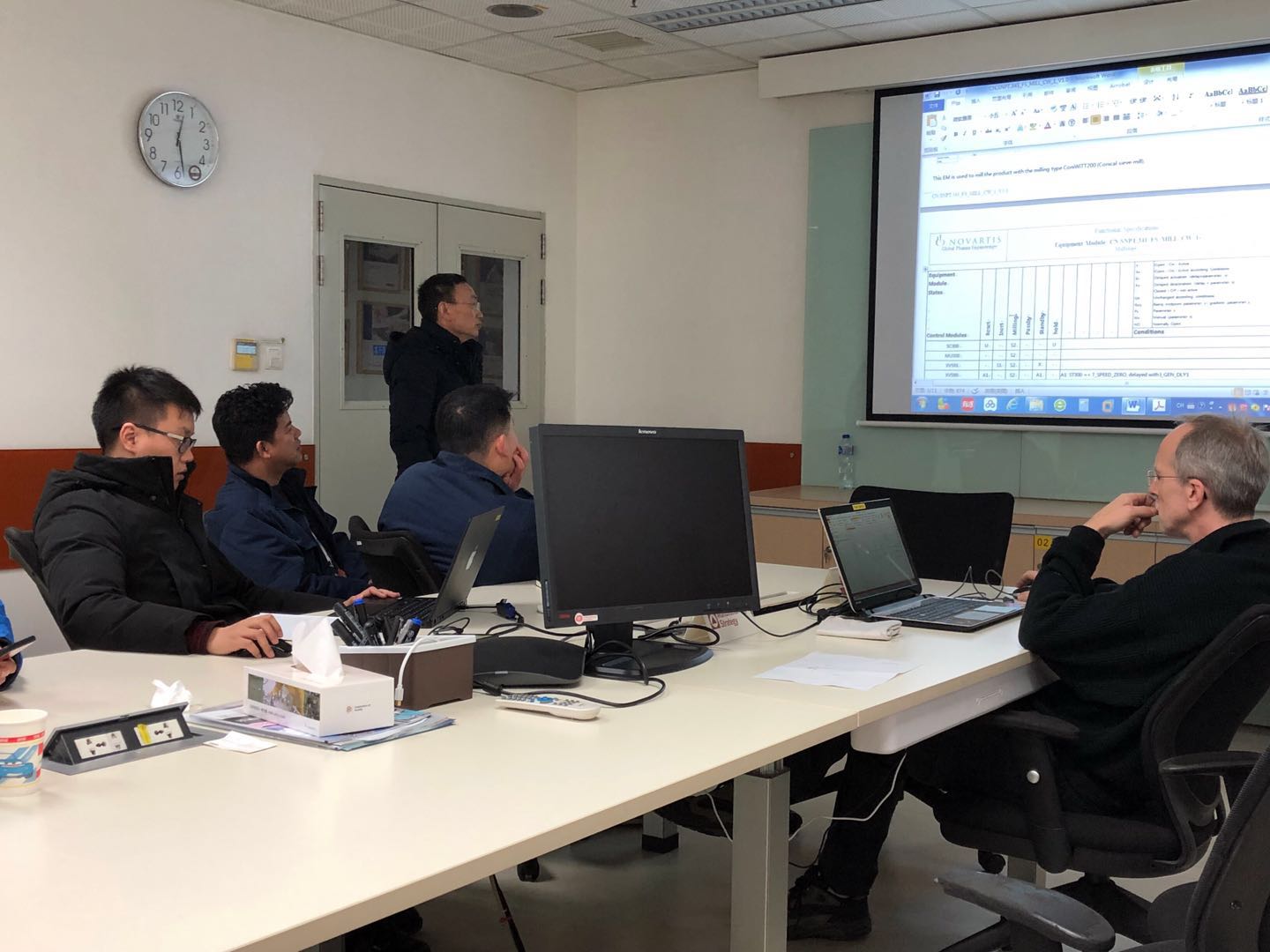
Novartis Pharmaceuticals Suzhou Continuous Manufacturing Technology (CMT) Project
This project represents a milestone as Novartis applies newly developed continuous manufacturing technology for the first time in China. The significant importance of this project lies in transforming the traditional batch production mode of pharmaceutical companies into a continuous production mode, which greatly enhances the production efficiency, reduces costs, and improves quality stability in the pharmaceutical industry. The main technical challenges are focused on clarifying the process understanding and program coding of control modules (EM) for temperature control, pressure control, material transfer, etc., in the new type of continuous reaction vessel (pipe-style) under continuous production mode.
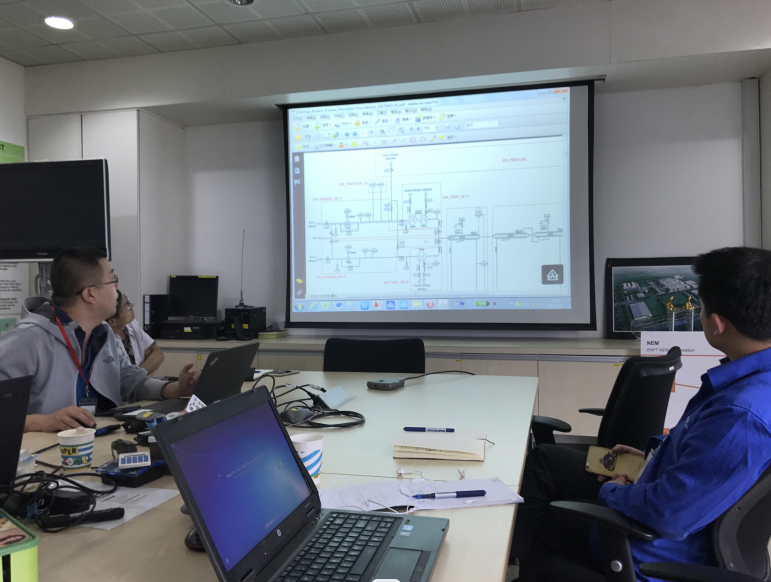
Novartis Pharmaceuticals Suzhou Rooster Continuous Transformation Project
This project aims to add new drug production lines to Workshops A1 and A2 and introduce a fully imported Milling & Blending powder grinding and separation conveying system, which will undergo GMP validation according to FDA standards. The main technical challenges lie in the process digestion and program coding of control modules (EM) for powder conveying, solid material grinding, pressure control, etc., in the Milling & Blending system. A formulation (Recipe) will be created to enable one-click start and achieve fully automated production. It will also generate reports and data that comply with the data integrity requirements defined by CFR21 PAR11.